احیای مستقیم پودر سنگ آهن بر پایه هیدروژن (به اختصار HYFOR) اولین فرایند احیای مستقیم جهان برای کنسانتره سنگ آهن حاصل از فرآوریِ آن است که دیگر نیازی به پیشپالایشهایی نظیر (Sintering) یا گَندِلهسازی (Pelletizing) ندارد. این فناوری نوآورانه، بر بستر تجارب ارزشمند حاصله از فرایندهای Finmet و Finex شرکت Primetals Technologies توسعه یافته و قابلیت بهکارگیری بر روی تمامی انواع کنسانترههای فرآوریشدهی سنگ آهن را داراست. HYFOR قادر است با ۱۰۰ درصدِ مواد اولیهای با ابعاد ذرات کمتر از ۰.۱۵ میلیمتر کار کند و حداکثر اندازهی دانه تا ۰.۵ میلیمتر را نیز میپذیرد. بهواسطهی سطح ویژه (Large Particle Surface) بالای ذرات، این فرایند میتواند به نرخهای احیای بالا در دما و فشار پایین دست یابد.
در آوریل سال 2021، پایلوت نیمهصنعتی احیای مستقیم پودر سنگ آهن با هیدروژن (HYFOR) که توسط شرکت پریمتالز تکنولوژیز ساخته شده است، در سایت فولادسازی فوستالپاین در شهر دوناوویتز اتریش به بهره برداری رسید و اولین آزمایش ها را با موفقیت انجام داد. این آزمایشها با کنسانتره های مختلف سنگ آهن انجام شد. استفاده از ۱۰۰ درصد هیدروژن به عنوان عامل احیاکننده، ردپای CO
2 را تقریباً به صفر کاهش داد.
[caption id="attachment_60354" align="aligncenter" width="576"]
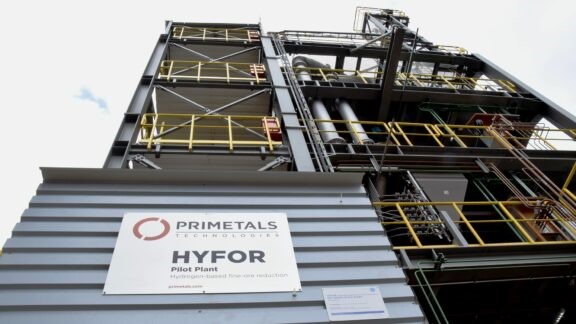
شکل ۱: پایلوت احیامستقیم HYFOR واقع در کارخانه فوستالپین اتریش[/caption]
کارخانه آزمایشی HYFOR از اولین فرآیند احیای مستقیم برای پودر سنگ آهن در جهان استفاده می کند که نیازی به فرایند گندلهسازی ندارد. این فرآیند به معنای کاهش هزینه های سرمایه گذاری (CAPEX) و هزینه های عملیاتی (OPEX) است و HYFOR تنها فرآیندی در جهان است که قادر به فرآوری پودر کنسانتره سنگ آهن با ۱۰۰ درصد اندازه ذرات کمتر از ۰.۱۵ میلیمتر و انواع مختلف سنگ آهن از جمله هماتیت و مگنتیت است که توسط مشتریان مختلف پریمتالز تکنولوژیز در سراسر جهان تامین می شود. کارخانه احیای مستقیم با طراحی مدولار ساخته خواهد شد که امکان مقیاسسازی سفارشی برای مشتریان برای کارخانه های فولاد با هر اندازه ای را فراهم می کند.
عامل احیای اصلی در این فرآیند، هیدروژن است که میتواند به صورت ۱۰۰ درصد از منابع تجدیدپذیر تامین شود. همچنین امکان استفاده از گازهای غنی از هیدروژن نظیر خروجی تجزیه حرارتی گاز طبیعی یا ریفرمرهای بخار متعارف نیز وجود دارد. استفاده از هیدروژن به عنوان عامل احیا کننده منجر به کاهش چشمگیر کربن و حتی دستیابی به ردپای کربنی صفر در فرآیند تولید میگردد.
محصول نهایی این فرآیند، آهن اسفنجی داغ (HDRI) است که میتواند به طور مستقیم به بخش ذوب پایین دستی، مانند کوره قوس الکتریکی (EAF) منتقل شود و یا برای تولید آهن بریکت داغ (HBI) بازارپسند مورد استفاده قرار گیرد.
راهحل پریمتالز تکنولوژیز برای حل چالش کاهش کربن در آهنسازی
این فناوری تحولآفرین، گامی بزرگ در راستای تولید فولاد سبز و کاهش انتشار گازهای گلخانهای در صنعت فولاد به شمار میرود. این شرکت متعهد است تا با توسعه راهحلهای نوآورانه و پایدار، به رهبری صنعت فولاد در مسیر دستیابی به آیندهای کمکربن کمک نماید.
با توجه به تشدید الزامات کاهش کربن در صنعت فولاد و گسترش روزافزون کورههای قوس الکتریکی (EAF) در سطح جهان، پیشبینی میشود تقاضا برای آهن اسفنجی (DRI) و بریکت گرم آهن اسفنجی (HBI) همچنان با رشدی چشمگیر روبرو باشد. در حال حاضر، تمامی فناوریهای موجود جهت تولید DRI یا HBI مستلزم توده سازی مواد اولیه، مانند گندلهسازی، هستند. از سوی دیگر، تولیدکنندگان فولاد با چالش کاهش کیفیت سنگ آهن مواجهاند که ضرورت فرآوری این ماده معدنی را بیش از پیش ضروری میسازد. دستیابی به تولید فولاد، با نشر کربن صفر، مستلزم بهرهگیری از فرآیندی است که عمدتا از هیدروژن (H
2) استفاده نماید. فرآیند نوآورانه HYFOR، پاسخی جامع به تمامی این نیازمندیهاست.
نگاهی دقیقتر به کارخانهی آزمایشی HYFOR
کارخانهی آزمایشی HYFOR از سه بخش اصلی تشکیل شده است: واحد پیشگرمایش-اکسیداسیون، واحد تصفیه گاز، و واحد احیای اصلی
در واحد پیشگرمایش-اکسیداسیون، کنسانترهی پودر سنگ آهن تا دمای تقریبی ۹۰۰ درجه سانتیگراد گرم شده و سپس به واحد احیا منتقل میگردد. گاز احیاکننده، که ۱۰۰ درصد هیدروژن است، به صورت برونسپاری از یک تأمینکنندهی گاز تأمین میشود.
یک سیستم غبارگیری خشک، غبار را جهت جلوگیری از انتشار آلایندهها در فرآیندهای مرتبط، جمعآوری و بازیافت میکند. آهن اسفنجی داغ (HDRI) پس از خروج از واحد احیا با دمای تقریبی ۶۰۰ درجه سانتیگراد، قبل از خنک شدن و تخلیه از کارخانهی آزمایشی HYFOR، سرد میگردد. در مرحلهی بعدی، یک واحد تست بریکتسازی داغ برای تولید آهن بریکت داغ (HBI) به این مجموعه اضافه خواهد شد.هدف از راهاندازی کارخانهی آزمایشی HYFOR، تأیید این فرآیند پیشگامانه و استفاده از آن به عنوان یک مرکز تست است تا بتوان بر اساس دادههای حاصل، مقیاس کارخانه را برای احداث یک نمونهی اولیه صنعتی در گام بعدی توسعه، ارتقا بخشید.
میدرکس با ۱۰۰ درصد هیدروژن
در صورتی که قرار باشد هیدروژن به طور دائم به عنوان تنها عامل احیا کننده مورد استفاده قرار گیرد، ریفرمر گاز طبیعی را می توان با یک گرمکن گاز احیا جایگزین کرد. H
2 طی فرآیند احیا به H
2O تبدیل شده و در اسکرابر گاز بالایی (Top Gas Scrubber) متراکم می شود. از آنجایی که هیچ منبعی از مونوکسید کربن در حلقه فرآیند وجود ندارد، نیازی به سیستم حذف CO
2 نیست. این فرآیند برای احیا به ازای هر تن آهن اسفنجی (DRI) تقریباً به Nm³ ۵۵۰ هیدروژن نیاز دارد. علاوه بر این، برای هر تن DRI حدود Nm³ ۲۵۰ H
2 برای گرما نیاز دارد که می توان آن را با سایر منابع انرژی تأمین کرد.
قابلیت کار با سنگ آهن کمعیار
فرایند HYFOR ضمن کاهش چشمگیر انتشار CO
2، به تولیدکنندگان در مقابله با چالش کاهش کیفیت سنگ آهن که اخیراً تشدید شده است (منجر به نیاز بیشتر به فرآوری سنگ آهن میشود) کمک میکند. افزایش تقاضا برای گندله سنگ آهن در کورههای بلند و کارخانههای احیای مستقیم، منجر به افزایش قیمت سنگ آهن، به ویژه گندله شده است. با بهرهگیری از HYFOR، تولیدکنندگان قادر خواهند بود مستقیماً از ریزدانهی کنستانتره سنگ آهن استفاده کنند.
اخلاق رسانه ای : استفاده از مطالب با ذکر منبع "چیلان آنلاین" مجاز است .