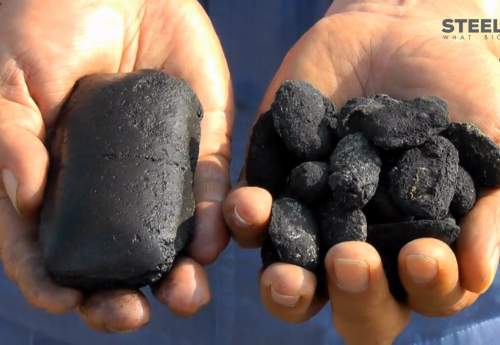
Rising scrap consumption in China is leading steel mills to set up RHF to extract zinc and iron oxide from the dust and slime
A paper authored by five experts published in the journal ‘Metals and Mining’ in March 2017 notes that as a developing economy, China has had limited amounts of obsolete (or post-consumer) scrap to use as a material in steelmaking. However, as the country’s products and infrastructure enter the replacement phase, the growing availability of obsolete scrap is likely to fuel a shift from steelmaking based on BOF to EAF technology that relies heavily on scrap. In time, this shift will have a significant impact on scrap consumption trends both in China and globally. This is substantiated by the fact that the China Association of Metal Scrap Utilization (CAMU) figures reveal that as much as 60 million tons of scrap was used by Chinese IFs in 2016. Moreover, demand for steel scrap used in steelmaking in China rose from 90.1 million tons in 2016 to 147.9 million tons in 2017.
This increased demand for scrap is reflective of a long-term commitment on the part of Asian giants such as China – hope India, too, will be catching up fast – to embrace new-age recycling technologies in steelmaking as resource efficiency has become the buzzword in the global steel industry today.
Zinc from EAFD: A Path-breaking Technology
Most steel products, for example automobiles and even furniture with white surfaces, are galvanized with a thin solution of zinc to make them corrosion-resistant. Scrap iron and steel are mostly recycled in EAFs where volatile as well as precious constituents like zinc, iron and lead are driven off as fine particles and gases. This Electric Arc Furnace Dust (EAFD) that needs to be filtered from the flue gases generally contains between 20% and 25% zinc and 25% to 30% iron, both of which occur largely as oxides.
In order to recover the zinc and iron – the latter is valuable as it could again be fed into the furnace – steel mills need processors to recover precious metals from EAFD. At historical zinc prices, the recovery of zinc from EAFD has not been possible without a subsidy — it has no value and is, therefore, considered to be a waste. Since it also contains traces of toxic elements such as cadmium, arsenic and mercury, it is classified as a hazardous waste. EAFD has been processed for many years using the Waelz kiln technology but this does not recover the iron, so the residue from the process is still a waste. Moreover, the cost of landfill, especially in the developed countries, is prohibitively high. In this context, the breakthrough technology is recovering the zinc, iron and lead by using a Rotary Hearth Furnace (RHF).
?”RHF: A ‘Game Changer
RHF technology uses pulverized coal as a reducing agent and coal gas as the fuel. Carbon-contained pellets, too, can be used. This fast direct reduction device is currently the most preferred when it comes to treating and recovering zinc and lead-contained dust.
The two principal functions of RHF are: treating steel plant dust containing zinc and special or hard-reducing iron ore such as V & Ti-contained iron ore, red soil nickel ore, hematite and limonite; and treating ferrous slag like copper slag and nickel slag and smelting iron making.
Chinese Companies Are Catching Up RHF
Chinese mills are catching up RHF technology in order to get maximum value from steel wastes. In June, 2015 Yanshan Iron and Steel of the Hebei Iron and Steel Group successfully accomplished the hot run test of the production line of its RHF. Currently, the production line has reached its designed output, production status is stable and every working procedure is running well. Research carried out by the China-based Chongqing Iron and Steel Design Institute (CISDI) shows the plant can dispose of about 200,000 tons of dust from the BF and RHF and obtain about 140,000 tons of metalized pellets, 5,000 tons of zinc oxide dust and 130,000 tons of steam, thereby achieving a high economic and environmental value.
Technical knowhow is fast gathering momentum, as is evident from the way China is investing in recycling technologies. It deserves mention that the Chinese state-owned enterprise, Central Iron & Steel Research Institute (CISRI) has carried out many successful RHF experiments as regards dust, iron ore and ferrous slag treatments. The results have been impressive. Moreover, CISRI has built equipment for semi-industrial experiments. It has finished the Rizhao RHF production line, which shows noteworthy achievements in terms of low cost, quality production and productivity volumes. It has treated 2×۰.۲ million tons of zinc-bearing dust each year and the metalized pellets are used as converter coolants, while the zinc-rich dust is sold out. The RHF uses producer gas as fuel, and the exhaust system is equipped with air and .coal gas heat exchanger
Cutting-edge Technologies
It is just a matter of time before such path-breaking technologies are adopted in other parts of the world. To ensure resource efficiency and to sustain manufacturing economies of scale, steel industry experts are relying on recycling technologies more than ever before.
Want to explore the many facets of RHF and other ingenious technologies? Make sure you attend SteelVia- The Global Steel Innovations Forum, where Dr Xu Haichuan, Professor at the Department of Advanced Material, China Iron and Steel Research Institute (CISRI), will deliver a thought-provoking address on the glittering future of RHF technology.

محمدکاظم صباغی هرندی
مدیر ارشد خدمات فنی و پشتیبانی شرکت فولاد مبارکه

مهندس طهمورث جوانبخت
مدیرعامل شرکت مجتمع فولاد خراسان

عطاالله معروفخانی
مدیرعامل شرکت فولاد هرمزگان

اکبرگلبو
مدیرعامل شرکت بینالمللی مهندسی سیستمها و اتوماسیون(ایریسا)

اردشیر فاضلی
مدیرعامل شرکت بازرگانی معادن و صنایع معدنی ایران (ایمیکو)