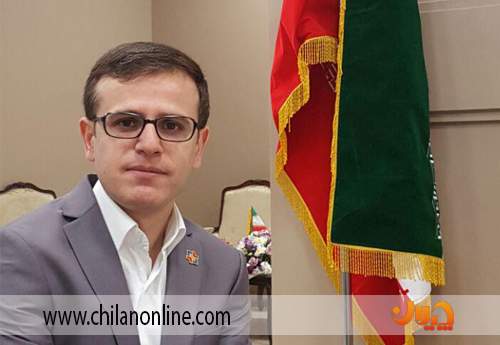
یکی از راه های تولید گازهای سنتز (مخلوط هیدروژن و مونوکسید کربن) فرآیند ریفرمینگ ترکیبات هیدروکربنی از قبیل گاز طبیعی، متان، پروپان و … با اکسنده هایی مانند H۲O یاCO۲ است. این واکنش گرماگیر بوده و نیاز به کاتالیست برای تسریع واکنش و انجام میزان درصد تبدیل مطلوب خوراک دارد. در واحدهای احیاء مستقیم سنگ آهن و تولید آهن اسفنجی، از این فرآیند استفاده شده و گاز ریفرم شده غنی از گازهای سنتز یا گازهای احیاء کننده که ریفرمر را ترک می کند، برای احیاء اکسید آهن به آهن فلزی تولید می شود. از این رو کاتالیست ها را می توان قلب تپنده واحدهای احیاء در نظر گرفت که عملکرد صحیح آنها در ریفرمر می تواند کیفیت و مقدار لازم جهت تولید مقدار مورد نیاز آهن فلزی را فراهم کند.
شکل ۱-تصویر کاتالیست خنثی(سمت راست)، نیمه فعال(وسط) و فعال(سمت چپ) مورد استفاده در ریفرمر مدول ۱ شرکت فولاد خوزستان
کاتالیست های ریفرمینگ احیاء مستقیم تولیدی این شرکت در اواسط اسفند سال ۱۳۹۵ در ریفرمر مدول ۱ شرکت فولاد خوزستان شارژ گردید و از آن تاریخ با عملکرد بسیار مناسب در حال سرویس می باشد. در این گزارش سعی شده است که به بررسی عملکرد این کاتالیست ها در دوره ۸ ماهه از بارگذاری آنها درون ریفرمر تا کنون پرداخته شود.
یکی از مهمترین پارامترهای موثر بر روی ترکیب درصد گاز تولیدی یا همان گاز ریفرم، ترکیب درصد اجزاء گاز خوراک (فیدگس) و خصوصاً اکسیدکننده های H۲O یاCO۲ است. وجود مقادیر اکسیدکننده های پایین سبب تشکیل کک و غیرفعال شدن کاتالیست ها شده و از طرفی وجود اکسید کننده های اضافی در گازهای ریفرم شده به واکنش های احیا سنگ آهن آسیب می رساند. به همین دلیل به منظور بهره برداری از ریفورمر میدرکس نیاز است که دقت لازم در نسبت های اکسیدکننده به مقدار گاز طبیعی صورت پذیرد. تنظیم این مقادیر از طریق میزان دبی حجمی گاز طبیعی و دمای گاز پروسس (گاز چرخشی در واحد) صورت می گیرد. بر خلاف واحدهای پتروشیمی، برای تولید گاز احیاکننده با کیفیت بالا در واحدهای احیاء مستقیم سنگ آهن، نسبت اکسیدکننده به کربن پایین مورد نیاز است. شکل (۲) نسبت اکسیدان به کربن، CO۲/C و H۲O/C را در سه ماهه اخیر فیدگس مدول یک را نشان می دهد.
شکل ۲- تغییرات نسبت اکسیدان ها به کربن در Feed gas در هشت ماه اول راه اندازی.
در ادامه به بررسی کیفیت عملکرد هشت ماهه کاتالیست های تولیدی شرکت گسترش فناوری خوارزمی در این واحد پرداخته خواهد شد.
مقدار متان در گاز ریفرم شده
برای رسیدن به آنالیز مطلوب گاز احیایی عوامل بسیاری تاثیرگذار می باشد. بازه ۵/۰ تا ۱ درصد مطلوبترین دامنه برای میزان متان در گاز ریفرم است که به آن گاهاً Methane Slip نیز گفته می شود. شکل (۳) تغییرات متان و دمای گاز ریفرم را در هشت ماهه اخیر نشان می دهد. در چندین بازه زمانی محتوی متان در گاز خروجی بالاتر از ۱ درصد می باشد. با توجه به شکل (۳)، در بازه زمانی ۲۰ اردیبهشت تا ۱۰ خرداد، دما نسبت به حالت ایده آل به علل محدودیت های بهره برداری از سوی بهره بردار چندین درجه کاهش پیدا کرده است. این در حالی است که کاهش بسیار کم دما باعث افزایش متان در خروجی خواهد شد. بعد از مدتی مشاهده می شود که مقدار متان در خروجی ریفرمر به مقدار مطلوب خود رسیده است که دلیل آن رسیدن دما به حد مطلوب می باشد.
شکل ۳- تغییرات ترکیب درصد متان باقیمانده و دمای گاز ریفرم در هشت ماه پس از راهاندازی
بالارفتن میزان ترکیبات سنگین خصوصا بوتان در گاز طبیعی و به تبع آن در فیدگس، ریسک تشکیل کربن بر روی سطح کاتالیست را به شدت افزایش می دهد که برای این منظور نیاز است تا اکسنده بیشتری نسبت به کربن وجود داشته باشد. در ابتدای خرداد، محتوای ترکیبات سنگین(+C۲) موجود در جریان گاز طبیعی تا ۲۰ درصد افزایش پیدا کرده است و غلظت متان در گاز طبیعی به میزان ۸۰ درصد حجمی رسیده بود. در ابتدای خرداد شدت جریان گاز طبیعی نسبت به گاز پروسس کاهش پیدا کرده است تا بتوان نسبت فوق را کنترل نمود و اثر منفی افزایش +C۲ جبران شود.
در بازه زمانی ۲۴ خرداد تا ۱۰ تیر و همچنین از اوایل مرداد تا اواخر شهریور، مشاهده شد که میزان متان در گاز ریفرم شده بیشتر از یک می باشد. دلیل این امر وجود مشکل در مخازن سولفورزدا جهت کنترل سولفور (H۲S) در خوراک ورودی می باشد. میزان بالا رفتتن مقدار سولفور به عنوان یک عامل مسموم کننده کاتالیست در فیدگس به مقدار حتی بالاتر از مقدار طراحی مخازن سولفورزدا یعنی ppm30سبب کاهش فعالیت کاتالیست ها می شود در حالی که این میزان توصیه شده است که زیر ppm 5 تنظیم شود. البته لازم به ذکر است عملکرد کاتالیست در حالتی که میزان سولفور تا ppm10 تا ۱۵ کنترل شود مشکل چندانی ایجاد نخواهد نمود.
به طور متوسط، طول عمر مخازن سولفورزدا در این واحد چهار ماه می باشد که ورود گاز سولفوردار با غلظت بسیار بالاتر از حد معمول (به سبب وجود سولفور بسیار بالاتر از حد نرمال در سنگ آهن) از سمت گاز Process در این مدت، طول عمر آن را به میزان زیادی کاهش داده است که این می تواند دلیلی بر تغییرات متان باشد.
جدول (۱)، آنالیز گاز احیا بعد از راه اندازی مخازن سولفورزدای جدید را نشان می دهد. همانطور که در شکل (۳) مشاهده می شود، با توجه به توضیحات فوق، پس از وارد مدار شدن مخازن سولفورزدا، میزان متان خوبی قابل تنظیم و کنترل بوده و مقدار آن پس از سولفورزدایی کمتر از ۱ درصد که مقدار ایده آل متان خروجی است نگه داشته شده است.
جدول ۱- آنالیز سولفور گاز احیا در مدول ۱ بعد از راه اندازی مخازن سولفورزدا جدید
میزان تولید بر حسب تن بر متر مکعب کاتالیست
بررسی بیشتر عملکرد کاتالیست ها نیازمند مطالعه پارامترهای تولید در کل واحد می باشد. بر اساس تجربه واحدهای میدرکس، یک واحد تولیدی به ازای هر متر مکعب کاتالیست با تزریق اکسیژن به لاین باستل می تواند ۱.۰۸ تن آهن اسفنجی تولید کند، اما در صورت عدم تزریق اکسیژن تولید به ازای همان مقدار کاتالیست ۱ تن بر متر مکعب خواهد بود. بنابراین با توجه به حجم کاتالیست های موجود در تیوب ها که در این مدول عددی معادل ۸۱.۷ متر مکعب است می توان شاخص تولید واحد را محاسبه نمود.
با توجه به شکل (۴) که نمودار این شاخص در هشت ماهه اخیر را نشان می دهد، متوسط این شاخص در یک ماه آغازین کمتر از حالت مورد نظر بوده است که علت این امر ناکافی بودن فلوی گاز پروسس در آن مدت به سبب مشکل فنی کمپرسور بوده است. پس از توقف کوتاه مدت و راه اندازی مجدد این شاخص در میزان مورد نظر حاصل گردیده است.
شکل ۴- تغییرات شاخص تناژ تولید در هشت ماهه اول راه اندازی
توجیه دقیق تر منحنی بدست آمده در شکل (۵) را می توان در روند افزایش فلوی گاز پروسس مشاهده نمود. به دلیل مشکلات فنی کمپرسور مرحله دوم، رسیدن به فلوی نرمال گاز پروسس در این واحد با محدودیت مواجه بود. فلوی پروسس در بازه زمانی ذکر شده به تدریج افزایش یافته و در روزهای پایانی به حداکثر مقدار خود یعنی ۸۸۰۰۰ متر مکعب بر ساعت رسانده شده است.
شکل ۵- تغییرات فلوی گاز پروسس در هشت ماه اول راه اندازی
بنابراین با توجه به اینکه برای تولید یک تن آهن اسفنجی ۱۰۰۰ متر مکعب گاز پروسس مورد نیازست، در ابتدای تولید ظرفیت واحد متاثر از کمبود فلوی گاز پروسس بوده و با افزایش آن ظرفیت مورد نظر واحد بدست آمده است.
متالیزیشن آهن اسفنجی
طبق اهداف و برنامه ریزی های شرکت فولاد، میزان متالیزیشن یا خلوص آهن فلزی ۹۲ درصدی برای آهن اسفنجی نیاز مورد نظر فولادسازی را برآورده می کند و خلوص ۸۸ درصد به پایین مردود یا Reject محسوب خواهد شد. در شکل (۶) که داده های خلوص آهن اسفنجی هفت ماه اول راه اندازی را نشان می دهد، مشاهده می شود که خلوص آهن اسفنجی علیرغم مشکلات عنوان شده به نحو مطلوبی بالای ۹۲ درصد بدست آمده است. فراوانی داده های خلوص آهن بالای ۹۲ درصد در این بازه نشان می دهد، واحد علی رغم سرعت تولید مطلوب خود، آهن اسفنجی با میزان خلوص بالا را نیز تولید می کند که حکایت از بازدهی بالا و مطلوب واحد نیز دارد.
شکل ۶- متالیزیشن آهن اسفنجی در هشت ماه نخست راه اندازی
بنابراین با توجه به اطلاعات و مطالعه صورت گرفته روی بازه ای مشخص از عملکرد کاتالیست ها می توان گفت که کاتالیست های تولیدی شرکت گسترش فناوری خوارزمی به نحو بسیار مطلوبی جوابگوی نیاز واحد بوده و با توجه به داده های بدست آمده از واحدهای احیاء خصوصاً تجربه فولاد خوزستان از کاتالیست های خارج، کاتالیست های تولیدی این شرکت می تواند در شرایط برابر عملکردی کاملاً قابل رقابت و حتی بهتر از خود نشان دهد.
- تعمیرات بخش های مختلف فولاد خوزستان با موفقیت انجام شد
- اولویت شرکت فولاد خوزستان، تامین مواد اولیه از داخل کشور است
- وزیر صمت:بهرهبرداری از کارخانه زمزم سه فولاد خوزستان، گام اول فولاد سبز است
- هت تریکِ فولاد خوزستان در دهه فجر
- پیام تبریک مدیرعامل فولاد خوزستان در مورد تولید اولین محصول آهن اسفنجی کارخانه در آستانه افتتاح زمزم ۳
- فروش ۱۹۰هزار تن آهن اسفنجی فولاد خوزستان به صورت بلندمدت/برنامه ریزی بدون دغدغه تولید از مسیر بورس کالا
- مشاهده کنید: تولید نسل جدید کاتالیست های بهبود یافته صنعت فولاد برای اولین بار در کشور
- عملکرد خیرهکننده فولاد خوزستان در ۱۰ ماهه نخست سال جاری
- در روز دوم جشنواره ملی فولاد ایران، فولاد خوزستان دو تفاهم نامه همکاری امضا کرد

محمدکاظم صباغی هرندی
مدیر ارشد خدمات فنی و پشتیبانی شرکت فولاد مبارکه

مهندس طهمورث جوانبخت
مدیرعامل شرکت مجتمع فولاد خراسان

عطاالله معروفخانی
مدیرعامل شرکت فولاد هرمزگان

اکبرگلبو
مدیرعامل شرکت بینالمللی مهندسی سیستمها و اتوماسیون(ایریسا)

اردشیر فاضلی
مدیرعامل شرکت بازرگانی معادن و صنایع معدنی ایران (ایمیکو)

سید رسول خلیفه سلطانی
دبیر انجمن تولیدکنندگان فولاد ایران

مهندس مدنیفر
مدیرعامل شرکت اپال پارسیان سنگان